An Interview with Paul Moquin
PRESIDENT OF ISLAND AEROBARRIER,
VANCOUVER ISLAND
By: Paul Harrison
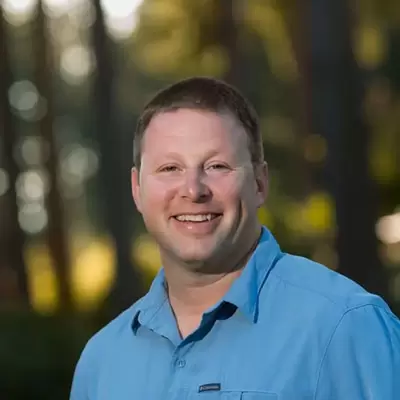
VANCOUVER ISLAND HOW LONG HAS YOUR COMPANY BEEN IN OPERATION? HOW DID IT GET STARTED? WHAT LED YOU TO FOUND/JOIN THE COMPANY?
Island AeroBarrier has been in operation for four years. Before this, I owned a residential and commercial building inspection company that also provided energy modeling, Island AeroBarrier has been in operation for four years. Before this, I owned a residential and commercial building infrared thermography, and indoor air quality testing. When I first heard about AeroBarrier, I knew that it would be a game changer for the building industry as the typical processes of getting a building tight can be time consuming and costly, with no guarantee of success.
In terms of energy savings, you get the biggest bang for your buck when you improve the airtightness of a building before you start to do other upgrades, such as windows or additional insulation. Air-sealing not only saves energy, but also makes the home more durable as it prevents moisture-laden air from getting into the wall assembly. Any moisture here can condense into water, and thus, support mold and rot.
TELL US ABOUT WHAT YOUR COMPANY DOES IN GENERAL?
Our focus is only on stopping the movement of air. In doing so, we are able to reduce energy waste, control moisture, reduce noise, and eliminate pathways for odors or pests.
EXPLAIN TO ME THE SEALING PROCESS? WHAT IS THE SEALANT COMPOSED OF?
The sealing process involves setting up nozzles inside of the building. After a preliminary blower-door test is done, the building is pressurized, and the nozzles atomize a water-based sealant that is both Built Green and Green Guard Gold certified. The air escaping from the building carries the sealant to the unwanted openings where it accumulates to form a seal. The progress is monitored on a computer in real time. Once the desired target has been achieved, a final blower-door test is completed, and a report is generated that shows the pre and post seal results. The average seal takes between two and three hours to complete. Once we are finished, people can go back in and resume their work.
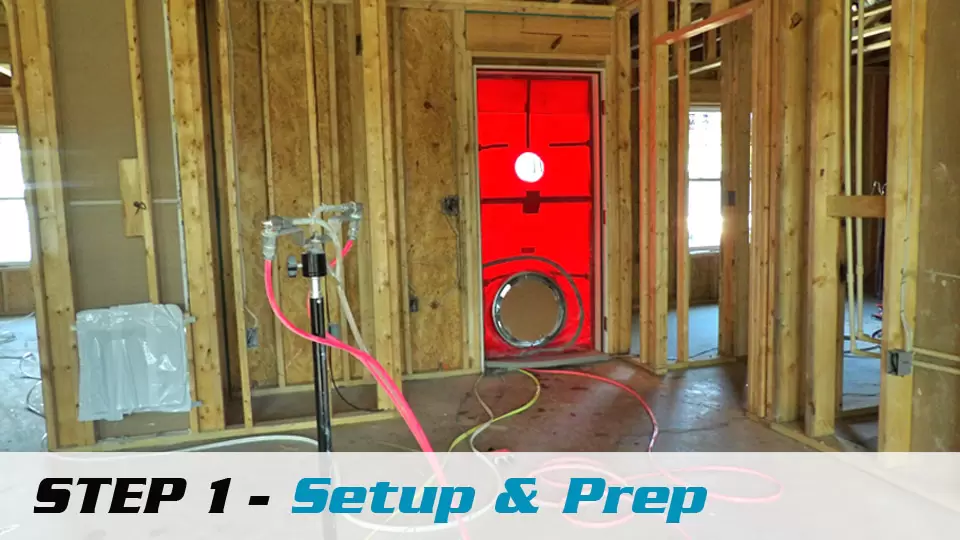
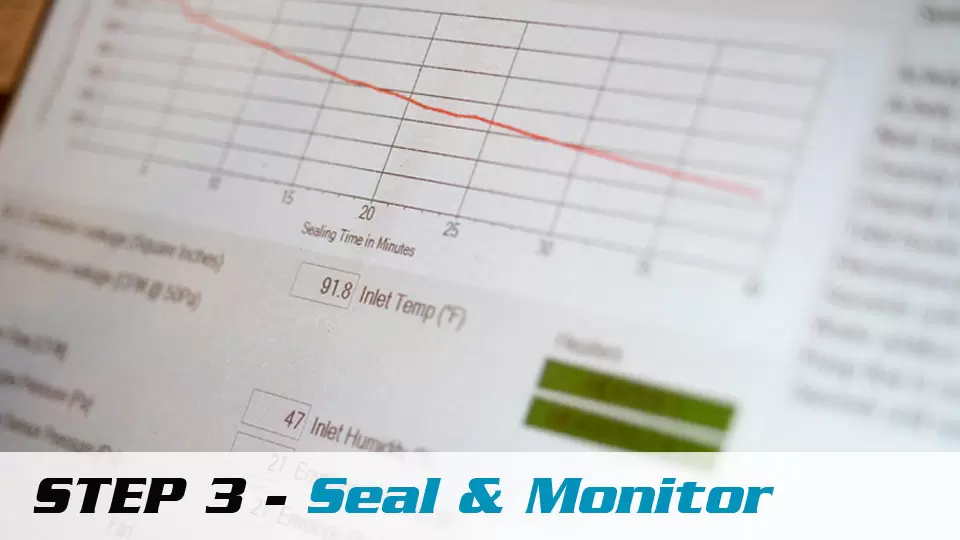

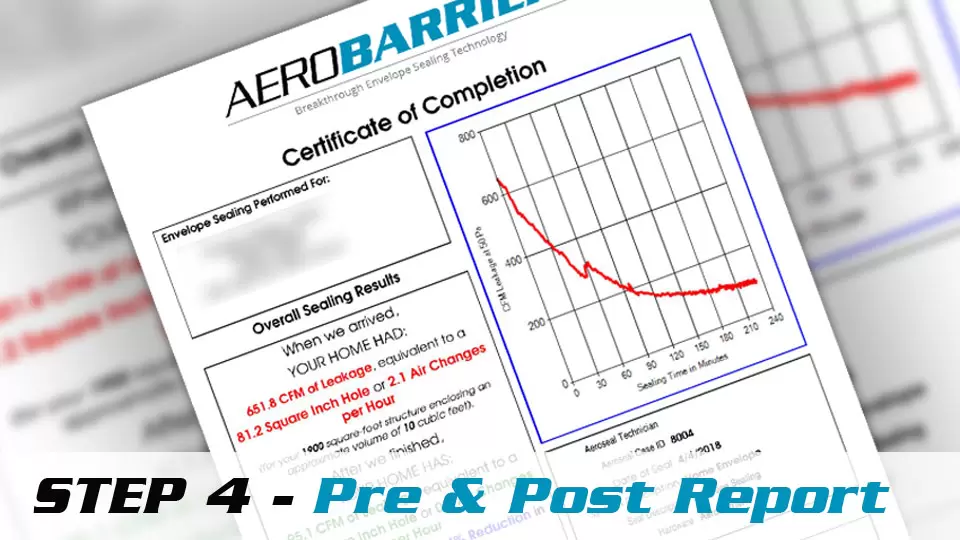
WHAT IS THE NATURE OF THE WORK YOU DO FOR J. ZSIROS CONTRACTING? DID YOU WORK WITH J. ZSIROS ON EITHER OF HIS 2022 GEORGIE AWARD WINNING PROJECT – EITHER CARRIAGE HOUSE ELEGANCE OR BLACK AND WHITE LUXURY (NET ZERO)?
Jim is a great builder that is always trying to raise the bar. We sealed the Black and White home for him, which led to his being awarded the Golden Blower-Door Award on account of its airtightness; he also won a table full of other awards for this project. We sealed the home down to 0.11ach50 (single point, positive pressure), which was easy as it was already at less than 1ach50 when we started. During the post construction test, it tested “as operated” at around 0.35 if I recall correctly. The increase in leakage is caused by differences in the test methods. We test with the intentional openings sealed and closed, and an “as operated test” does not do so.The additional leakage would be attributed to leakage at intentional openings, such as exhaust dampers.
ENVIRONMENTAL BOONS ASIDE, DO YOU HAVE A ROUGH ESTIMATE FOR HOW MUCH A PERSON CAN SAVE BY FINDING, AND FIXING, ENERGY LEAKS IN THEIR HOMES?
We are asked this a lot and it is a difficult question to answer as every home is different with regards to the utilities that they use (such as gas or electric), the rate that they are paying, and how leaky the place is to start. I have seen numbers that state that up to 30% of your heating/cooling energy use could be attributed to air leakage in older homes. Utility bills are, for the most part, a bunch of fees (storage, transportation, municipal fees, and taxes, tacked onto the energy that you use). The cost of the gas or electricity may only be 25% of your total bill.
The real benefit of air-sealing is the improved comfort that you will notice in a tight home or compartmentalized multifamily building that also has a good ventilation system, such as an HRV or ERV. A tight home is quieter. Sealing all of the gaps is like closing thousands of small windows to the outside or attached neighbors. The temperature remains more consistent, and the HVAC system does not need to kick in as often. By sealing the home or apartment unit, we are also able to stop pollen, smoke, and other pollutants from outside from entering. If you live in a multifamily building and can smell your neighbors’ cooking odors or smoke, then you are living in a building that is not well sealed.
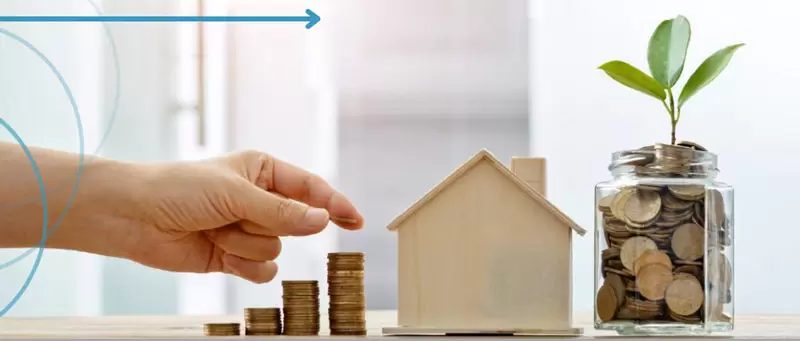
Leaking air transports a lot of moisture with it. This moisture can condense within a wall assembly and cause the structure to rot. This damage will eventually need to be repaired, and to do so will mean tearing the wall or floor assembly apart to remove, and then replace, the damaged materials.
We also see builders “value engineering” the cost of AeroBarrier into their builds. For example, by making the building very tight (with good ventilation), they are sometimes able to go with a lower cost option elsewhere. In one case, a builder was able to substitute triple glaze windows for double glaze windows. This was on a five storey, 60-unit apartment building, so the money saved on the windows was more than the cost to seal all the units.
CAN YOU APPLY THE SEALANT ON ANY HOUSE, OR DO YOU NORMALLY WORK ON NEW BUILDS OR HOUSES UNDERGOING MAJOR RENOVATIONS?
Most of the work that we do is for new construction, but we are seeing growth in the renovation market as more people are becoming aware of us. The majority of seals are done after drywall but before finishes are installed; we can, however, also seal finished but un-occupied homes. Sometimes this is done on existing homes when purchased before the new occupant moves in. Other times we are brought in to rescue a builder when they find out that they failed the blower-door test at final inspection. The downside of sealing a finished home is that there is a lot of preparation required to protect non-vertical surfaces so that our sealant doesn’t settle on them.
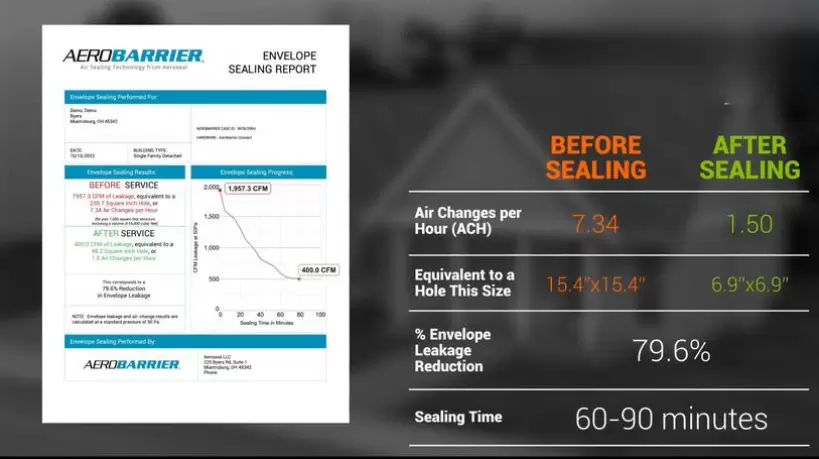
DO YOU HAVE ANY EXCITING NEW PROJECTS ON THE HORIZON, OR ANY OTHERS THAT YOU MIGHT HAVE JUST WRAPPED UP?
This past year has been an interesting one for us. A client was building a DNA lab and wanted to guarantee that contaminants could not get in. We also sealed a spray booth that is used for painting aircraft parts. The paint booth was inside of a building and people were complaining about the paint fumes leaking into the rest of the building. Sealing the booth solved the issue and, as a bonus, they said that the cost to operate it in the bake cycle had been greatly reduced. Once the furnace brought the booth up to temperature, it did not need to cycle on and off like it use to do prior to being sealed.
For more information on Island AeroBarrier, visit https://www.islandaerobarrier.ca/
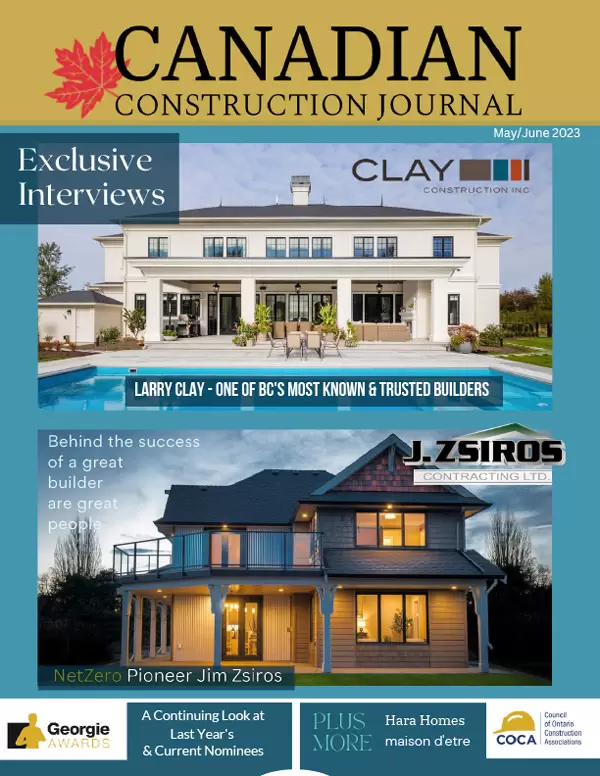